軽量素材の三次元加工に最適な
NCモデリング加工機を販売しています。
造形・試作・生産の現場を支える加工機をご提案します。
FRP・発泡材・樹脂などの軽量素材を対象とし、小型から大型まで幅広い加工サイズに対応可能な3軸加工機を販売しています。Zストロークの延長やATC(自動工具交換)本数変更など多様な用途に合わせたカスタマイズにも柔軟に対応。加工に使用する刃物やアングルヘッドを活用した側面加工など創造性が求められる現場を支える設備をご提案しています。
NCモデル加工機(テーブル1200×1200 / ATC12本)3軸
弊社が販売するNCモデリング加工機(3軸)は標準仕様をベースにカスタムする事が可能です。
お客様のご用途に合わせながら下記項目を組み合わせて仕様を決定します。(下記は一例)
テーブルサイズ 1200×1200 / 2500×1200 / 3000×2000 / 4000×2000
テーブル種類 バキュームテーブル / 製缶タップテーブル / T溝鋳物テーブル
主軸出力 3.7kw / 7.5kw / 11kw
主軸端形状 BT30 / BT40 / BBT40
ATC本数 12本 / 24本 / 48本
各軸ストローク テーブル端からの抜け量やゲージラインなど打合せ
その他 エアーブロー、オイルミスト、集塵システム、制御装置オプションなど
導入事例
事例01
鋳物用型枠 製造事業者様
背景
自社での鋳物製造において、木型や造形物を外注していたがコスト増や複雑形状への対応困難などが課題となっていた。
解決
NC加工機を導入した事で、複雑形状で修正が出る型枠の手直しもスムーズになり、外注コストも抑えられ製造工程を効率化することができた。
事例02
試作製品プロダクトモック 製造事業者様
背景
試作品の形状確認・デザインモデル製作を外注していたが、コスト増とリードタイムの長さが課題となっていた。
解決
社内加工への切り替えで試作のPDCAが加速。夜間も連続して加工することにより、納期・コスト両面で大きな効果を得た。
NCモデリング加工機(3800×2000mm/Zストローク800mm)
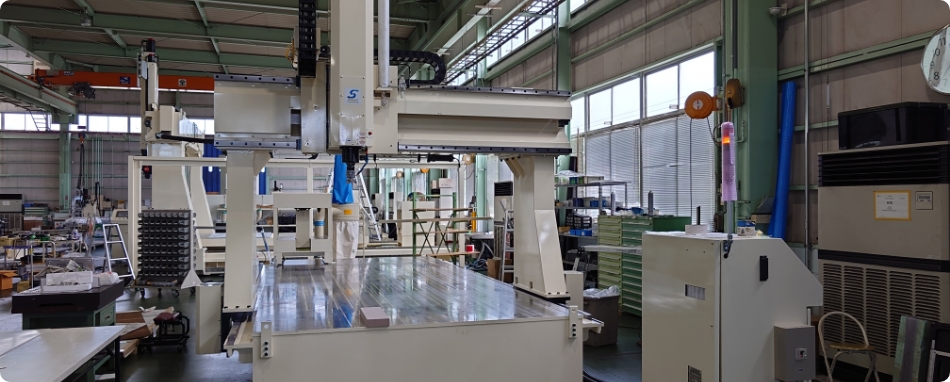
長手3800mm×幅2000mmの加工範囲と高さ800mmのZストロークにより、中型~大型の試作品や美術造形物にも対応可能な3軸モデル加工機です。CADCAMを活用した運用により、多様な形状の構造物を安定した精度を保ちながら削り出します。
導入事例
事例01
木型型枠 製造事業者様
背景
大型木型の製造依頼が入るとワークを分割して対応しなければならず納期もかかってしまい効率化悪かった。長期的に加工機を占有してしまうことで他の案件を外注しなければならない場合があった。
解決
加工範囲を大きくとったNCモデル加工機を導入したことで、一工程で加工をほぼ完結することができ、納期の短縮と工数の削減につながった。自社で対応できる時間も確保できたので利益率も向上した。
事例02
美術造形品 製造事業者様
背景
大型展示物の加工で分割が必要となり、継ぎ目処理や強度面で仕上がりに限界を感じていた。
解決
広い加工エリアと深さにより大型構造物を一体で削り出し可能に。完成度と意匠性の向上でクライアント評価が高まった。
大型3軸モデル加工機(4000×2000mm/Zストローク1200mm)
最大クラスの加工領域と1200mmのZストロークを備えた大型3軸モデル加工機。発泡材、ケミウッド、FRP、大型樹脂素材の削り出しや型枠加工など、高さと広さを要する加工に活用されています。一体成形に近い大きな造形を可能にし、複数パーツの分割や組み立て工数を大幅に削減。安定した駆動制御により、長時間加工でも精度を保ち、大型製品の製造に最適です。
導入事例
事例01
船舶部品 製造事業者様
背景
大型製品の加工は外注頼みでコストがかさみ、納期も予測しづらく、営業機会の損失につながっていた。仕上がりの確認も製品が出来上がるまでわからないことが多かった。
解決
高いZストローク対応の内製体制を整えたことで、リードタイム短縮と外注費30%以上削減を同時に実現した。手直しも容易にできるようになり最終製品の品質保持にもつながった。
事例02
テーマパーク装飾品 製造事業者様
背景
巨大造形物の一体加工が困難で、パーツ分割による接合トラブルや再加工の手間が大きな負担となっていた。
解決
高いZストロークと広範囲対応の加工により一体加工が可能に。強度・美観の向上と同時に作業工程の簡略化を実現した。データを分割する手間を最小限にすることができ組み立て工程の手間とコストを削減することができた。